Next Generation Mobility
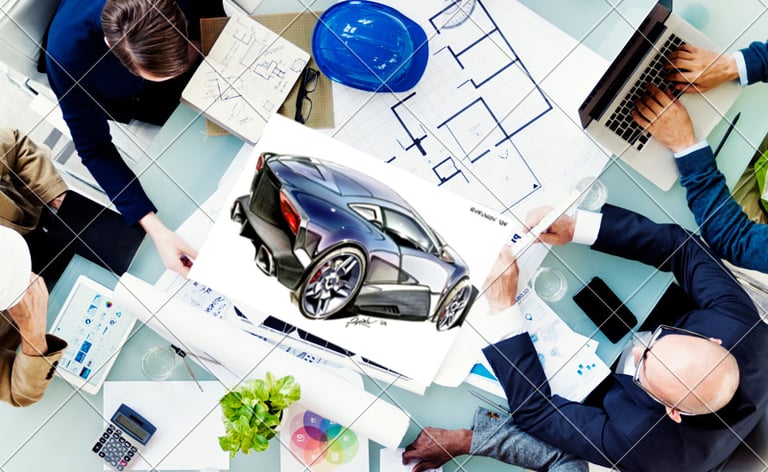
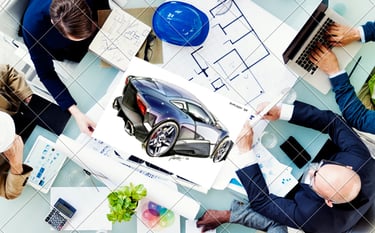
Building better vehicles is tough. Meeting user requirements, industry demands, cost targets, and government standards while maintaining quality poses unique challenges. Traditional methods are best suited to optimizing and ensuring performance under very specific conditions. Previously, taking into account the full range of variation in materials, manufacturing, and usage when designing new vehicles was a monumental challenge. Now it’s possible to rapidly explore design spaces, trace uncertainty through vehicle systems to get probabilistic performance estimates, and quickly and accurately calibrate any model to test data.
Battery Engineering
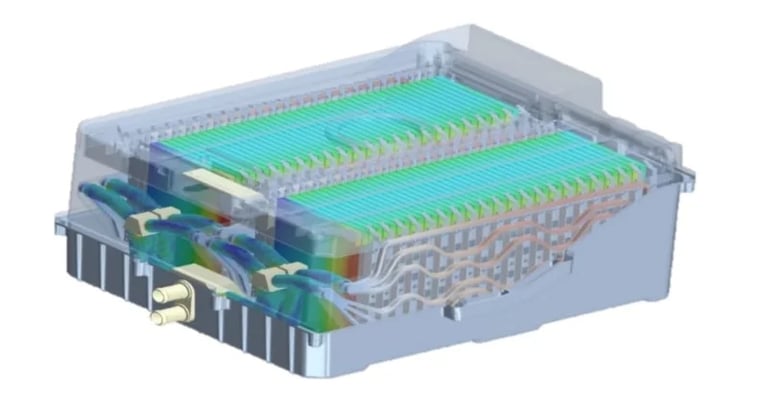
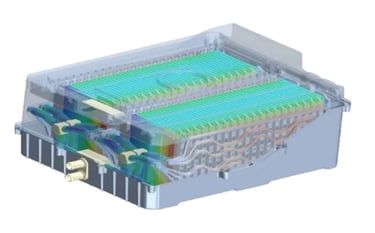
Batteries are the new fuel tanks in electric vehicles. They need to store as much energy as possible to minimize range anxiety, as well as maintain safety in case of unexpected events.
Batteries are highly complex systems, requiring advanced engineering methods at all levels: from chemistry to cell engineering, to module and pack engineering, and finally integration into full vehicles.
Drive Cycle Simulation
Pack Thermal Gradients Evaluations
Cell Selection Matrix
Passive and Active Cooling Strategies
Heat Sink Optimization
Rack Design for Energy Storage Units
Busbar sizing and Manufacturing Feasibilities
Fast Charge and Swappable Battery Designs
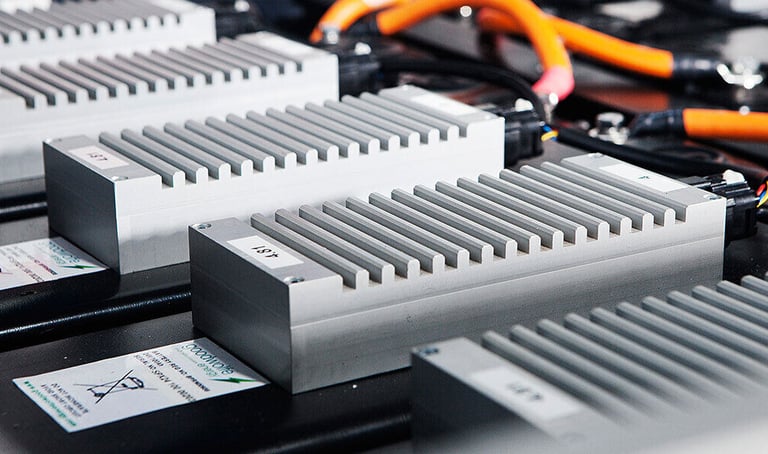

Rise of the Drones
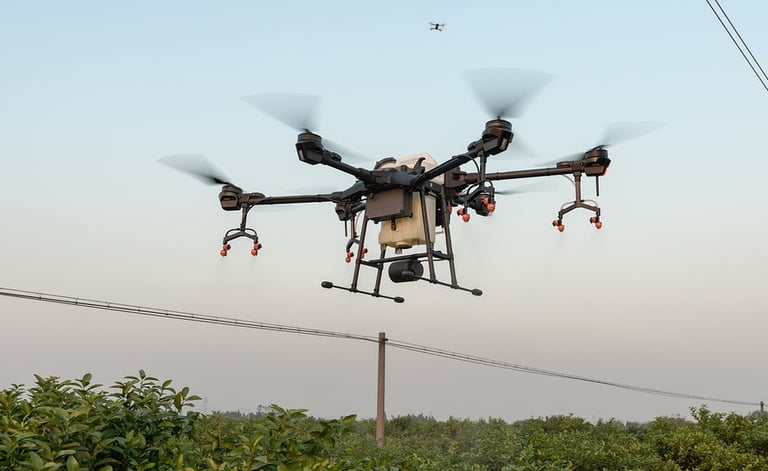
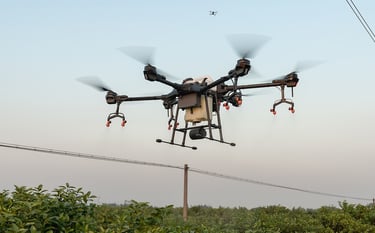
In the past decade, the broad spectrum of applications of these drones has received most attention which led to the invention of various types of drones with different sizes and weights.
Design and fabrication challenges of micro drones, existing methods for increasing their endurance, and various navigation and control approaches are delivered for the next generation drones.
Meeting standards and ensuring performance means accounting for uncertainty in all aspects of new designs. Gofinite allows deterministic models to be used to quantify, trace, and analyze the results and impacts of uncertainty throughout the design process.

Here are some key use cases
Drone Design Optimization:
Flight Time and Range Optimization: CAE simulation tools can help optimize drone design for maximum flight time and range. This involves using advanced CFD (Computational Fluid Dynamics) techniques to simulate and optimize the aerodynamics of the drone, ensuring efficient energy consumption and extended flight capabilities
Aerodynamic Simulation and Optimization:
CFD Analysis helps evaluate drone performance and stability under various flight conditions. This includes simulating airflow behavior, aerodynamic loads, and rotor-rotor interactions to optimize drone design for better efficiency and stability
Structural Analysis and Testing:
Drop Test and Vibration Analysis can simulate the structural integrity of drones. This helps engineers evaluate the durability and robustness of the drone's structure, ensuring it can withstand various environmental conditions
Thermal Management and Cooling:
Electronics Cooling: CAE simulation can be used to optimize thermal management and cooling systems within drones. This involves simulating heat transfer and fluid flow to ensure efficient cooling of critical components, such as batteries and electronics
Battery Design and Testing:
Battery Pack Design and Cooling Validation: CAE simulation can be applied to optimize battery pack design and validate cooling systems. This ensures efficient energy storage and safe operation of the drone
CONTACT US
If you're interested in hearing more about the way we work, have a business proposal, or are interested in opting a service, we'd love to hear from you.
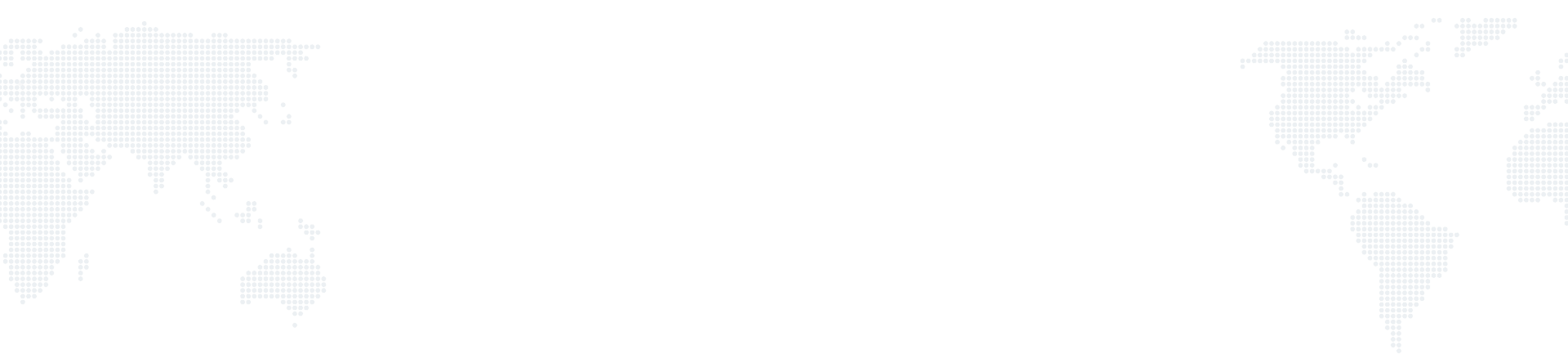
Gofinite Ventures LLP
LLPIN : AAU-5144